Crossrail - Hydrodemolition of Diaphragm Wall
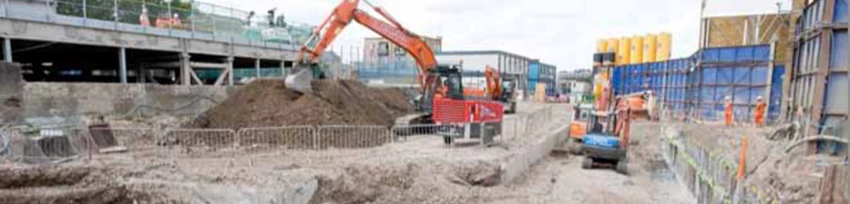
Hydrodemolition and concrete removal of diaphragm wall to access steel reinforcement
- Customer: Crossrail / Bam Nuttall Kier JV
- Service: Concrete hydrodemolition, cutting and selective removal
- Industry: Civil Engineering
When a joint venture of BAM Nuttall and Kier (BNK) needed help with the selective removal of concrete in the top 1 metre of a diaphragm wall on one of their Crossrail sites, they approached RGL for a solution using UHP water jetting. Like most concrete Hydrodemolition tasks, this would aim to leave steel reinforcements within the wall intact, ready to be integrated to a capping beam.
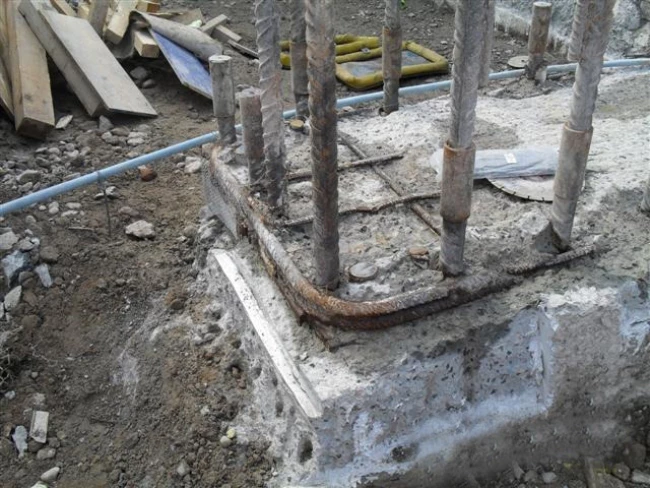
On previous projects, where similar height reduction was required, the use of percussive tools to break down the concrete resulted in a damaged edge at the cut-off line. This edge required extensive and costly concrete repair remedial work before the capping beam could be added.
Once all Health and Safety requirements for BNK were understood, RGL prepared a detailed Risk Assessment and Method Statement for approval, prior to commencement.
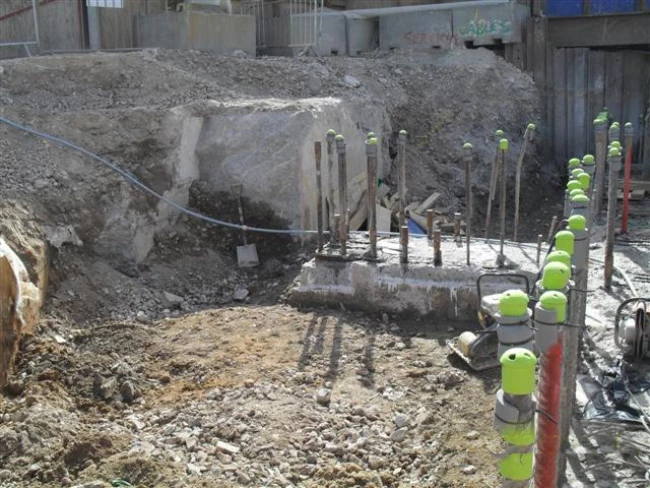
The work was undertaken within a confined 2m2 work enclosure, covered with a double layer of debris netting to eliminate the dangers of flying concrete on site. Acoustic panels were used to minimise noise and disruption due being in the vicinity of residential properties. The enclosure provided a safe area for the Hydrodemolition work to be undertaken, while ensuring the safety of other site workers in the immediate area.
RGL provided one trained jetting crew (2 qualified operatives) to undertake the work. It was agreed that the top portion of the diaphragm (approx. 600mm) was to be removed via the traditional hydraulic breaker method, as this would not affect the integrity of the wall, and the steel reinforcement to this level was not required for affixing the capping beam. This reduced the amount of concrete to be removed by Hydrodemolition and optimum progress could be made on this time critical operation.
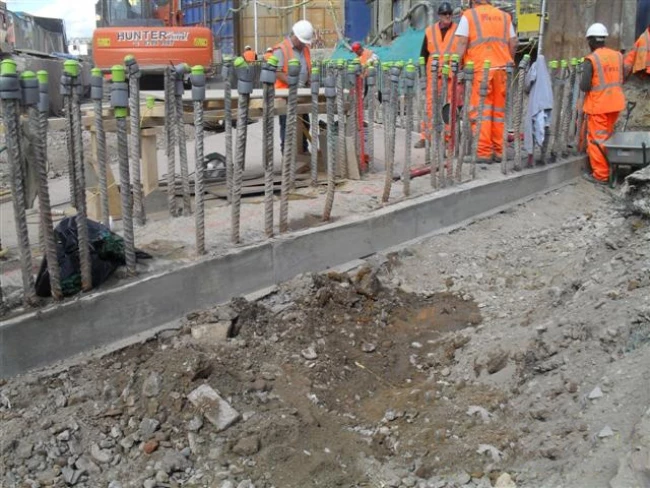
RGL were then able to concentrate on removing concrete from within the critical steel reinforcement, leaving it intact. The hydraulic breaker work was undertaken directly by BNK in a staged process, ensuring the next section of the diaphragm wall had been broken down, ready for jetting, typically to within 300mm of the proposed line cut.
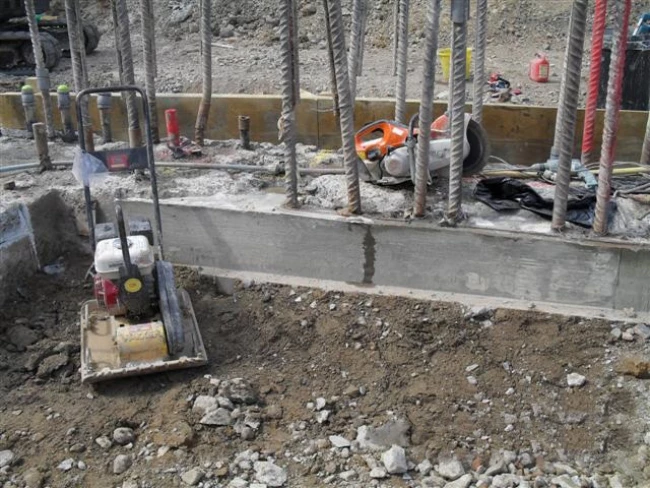
During the project BNK requested RGL to provide a second jetting team to satisfy an identical requirement to be undertaken on another BNK Crossrail site.
Iggy Hoey was the contact from BNK that RGL communicated and discussed the proposed changes to the works package with; “I found RGL to be very helpful and accommodating during this project. Once the scope of work was changed they were able to provide an additional jetting team when requested to ensure the project was completed on time and within the constraints imposed on BNK by our client”. The edge of the cut line was preserved, which avoided the need for costly concrete repairs. This enabled BNK to cap both walls as planned and move onto the next stage of the project in a timely manner.
Request a call back