Ponticelli Titanium Cutting: Ultra-High-Pressure Water Jet Solution
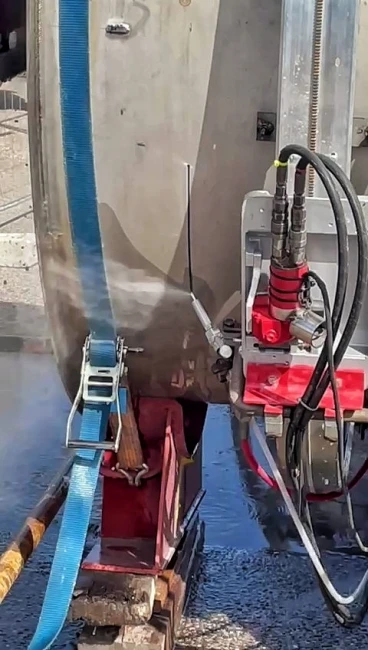
We (RGL) were contacted last year by “Ponticelli” with regards to providing an abrasive water jet cutting solution at their Client’s PVC plant in the centre of France. There has been manufacturing on this site for many years and we considered ourselves privileged to be given the opportunity to work with them on this, their latest innovation.
Due to the chemicals used in PVC production, some of the process pipework was manufactured from Titanium which has entirely different properties to the more standard metals which have traditionally been used. Titanium does not respond well to heat so cutting with flame or plasma was not an option. However, RGL’s “abrasive water jet cutting” system provided an excellent alternative.
Normally, titanium tubes are manufactured from flat titanium plate which is cut by abrasive water jet on an X Y axis table and then rolled to form the tube. In this case, the tubes had already been rolled so RGL’s specialist “on site” abrasive water jet cutting was required.
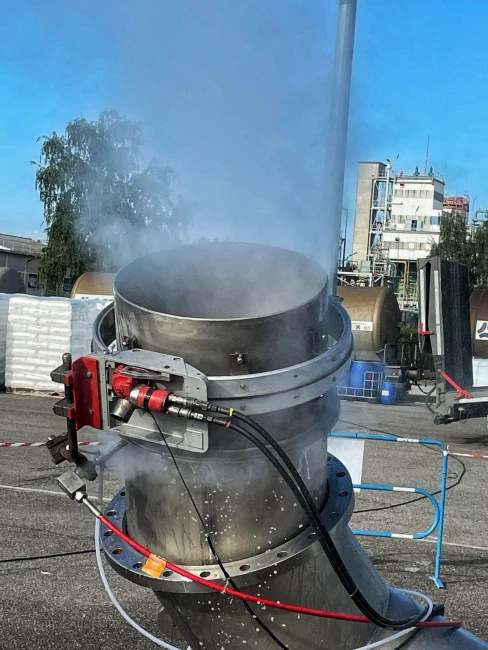
RGL’s task consisted of cutting 21 titanium tubes of diameters ranging from 600mm right up to 2,500mm. For the 600mm cuts we used a track which was fitted concentrically around the tube allowing the cutting head a full 360 degree rotation. In addition, the abrasive jet nozzle had to be set at a 30 degree angle to provide a “weld prep” on the cut end of the pipe.
The challenge came when cutting the larger diameter tubes which proved to be less stable than the smaller ones. This posed a problem with cutting accuracy due variations in tube concentricity. As the cutting nozzle was set at an angle, this variation created a “wavy cut end” of the pipe which made the client’s job of re-welding on a flange very difficult.
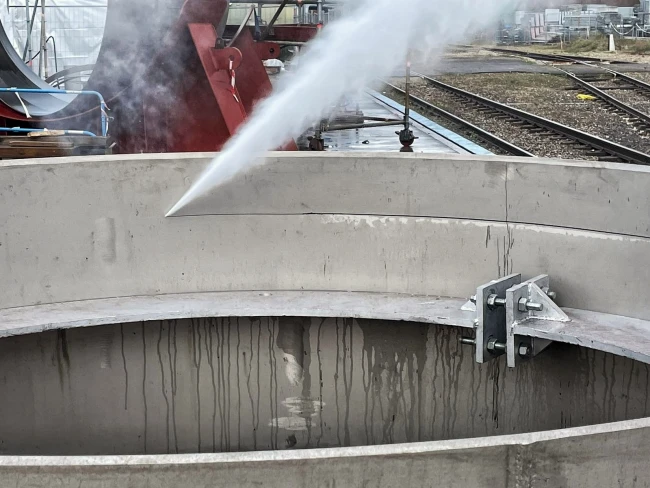
RGL and Ponticelli worked together to find a solution: Ponticelli devised and fitted a “form” inside the tube to hold it concentric and RGL deployed a different cutting rig which followed the exact diameter of the tube thus keeping the nozzle standoff distance consistent.
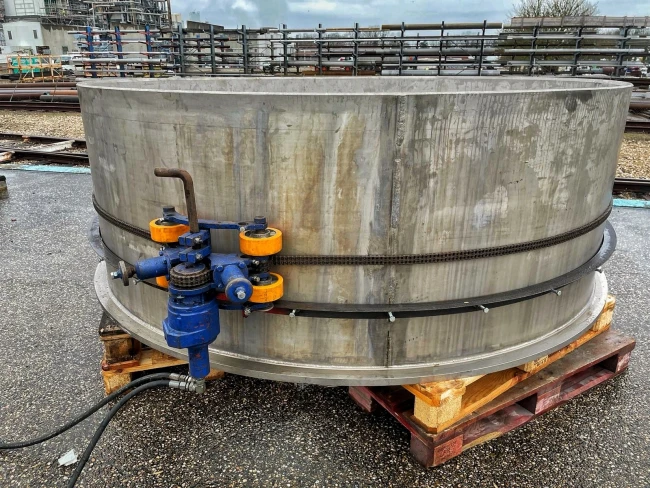
This successfully completed project was a steep learning curve for all involved but proved that when two professional teams work together, synergies can be created, barriers overcome and goals achieved.
We thank Ponticelli for the opportunity to work together and look forward to further collaboration in the future.
Request a call back