Bombay Sapphire - Underwater Pile Cutting of Sheet Larssen Piles from Around Ornamental Glass House
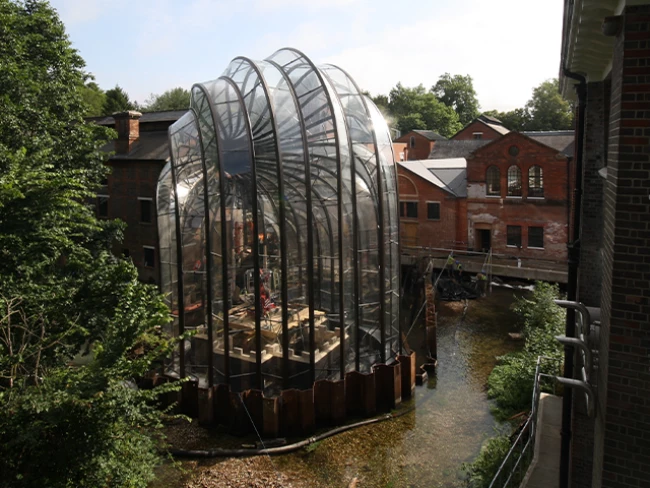
- Customer: Bombay Sapphire
- Service: Abrasive Water Jet Cold Cutting / Underwater Pile Cutting
- Industry: Food and Drink
When Mellor needed to remove several sheet larssen piles from around an ornamental glass house at the Laverstock Distillery, they called upon RGL to provide a water jetting solution to cut the piles 300mm below the river bed.
The cutting task involved removal of approximately 30 metres of Larsen piles surrounding a brand new ornamental glass house. It was further complicated as the glass house had been constructed in a river bed. The Piles had been installed as part of the construction phase and now required cutting off approximately 300mm below the river bed so as not to detract from the overall appearance of this beautiful glass structure in its natural setting.
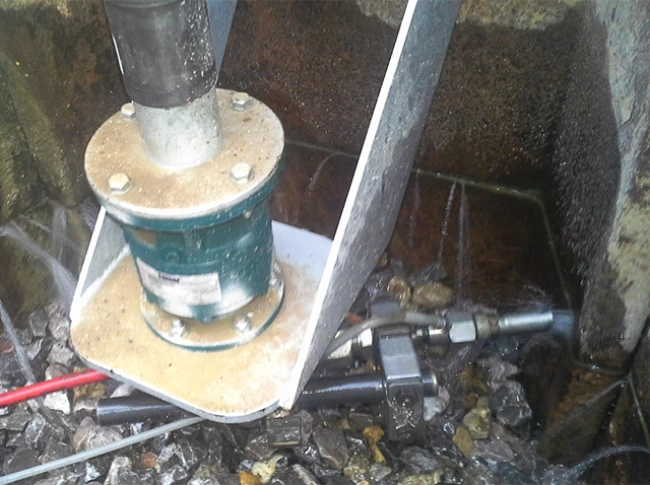
This posed a large number of questions, as the cutting work had to be achieved in a small area and it was essential no damage was caused to the glass construction they surrounded. Firstly RGL undertook a detailed site survey then held their usual project initiation meeting with the team to plan the task.
It was decided that a standard RGL straight abrasive water jet cutting track would need to be bolted to each group of Larsen piles to perform the horizontal cuts on the out-pan flat faces of the piles.
For the in-pan faces, some bespoke tooling would be required. It was decided a rotating nozzle holding device which could be adjusted to the required radius would be the best solution. The speed of rotation would need to be carefully set to ensure a complete cut was made on the thicker “clutch sections” as well as the thinner flat sections. In preparation for the works an RGL Technical Support Engineer attended site to prepare the required fixings to the piles. This was done by using a laser level and by drilling holes at a predetermined distance above the cut line, to match the tooling brackets that were being manufactured for the job.
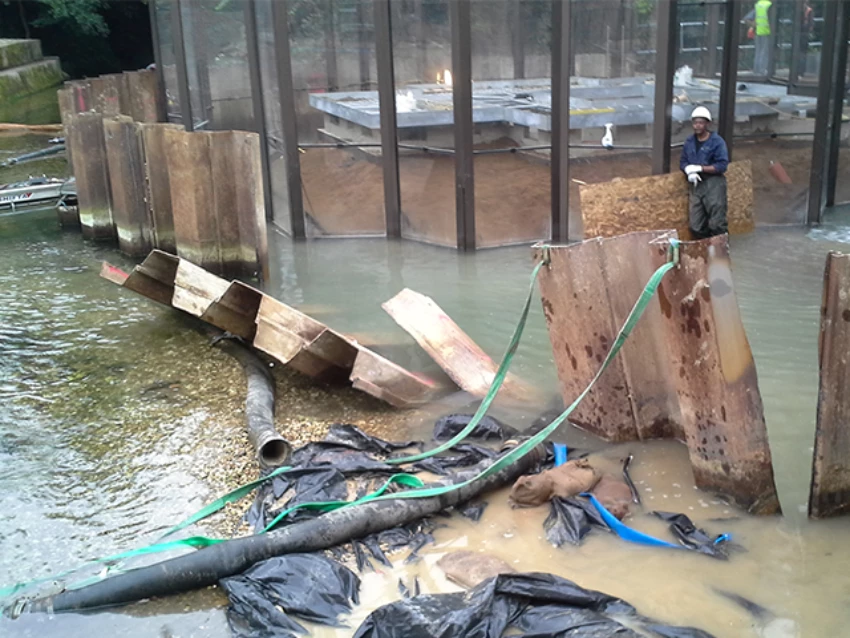
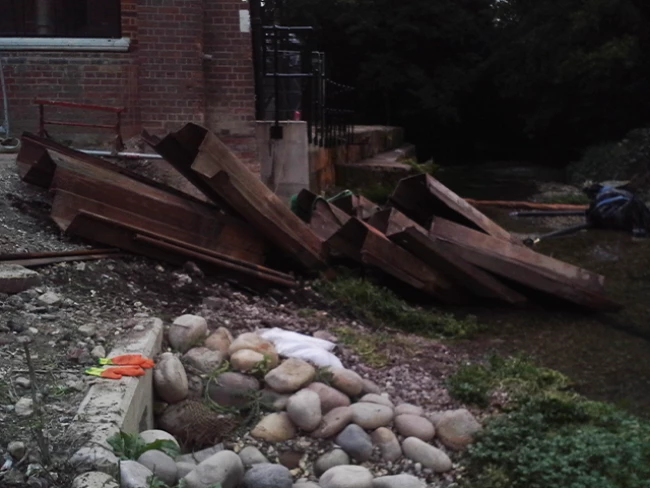
Upon arriving on site for the first day of cutting, RGL set up all the required equipment, and undertook a test cut along two number; flat out-pan pile faces and one in-pan section including two clutches. This allowed the correct cutting speed with the straight track and the rotating nozzle holding device to be set. After the successful test cuts were complete, work could continue, undertaking in-pan cuts from the dredged side of the piles – closest to the glass house. It was decided to start with these cuts as the in-pan cuts were the longest and hardest cuts to undertake as the jet had to pass through the thick clutch sections.
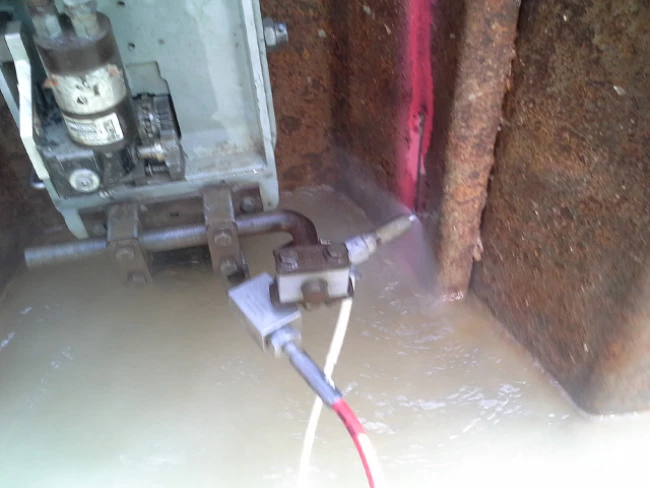
The cuts removed very little material and thus allowed only limited river water to pass back into the work area. Water level could be maintained within safe limits between the glass house and the piles, by the pumps which had been set up in advance.
The in-pan cutting involved 30 individual cuts. All cuts were made perfectly level and on line thanks to the careful marking out and drilling of fixing points which had been previously undertaken.
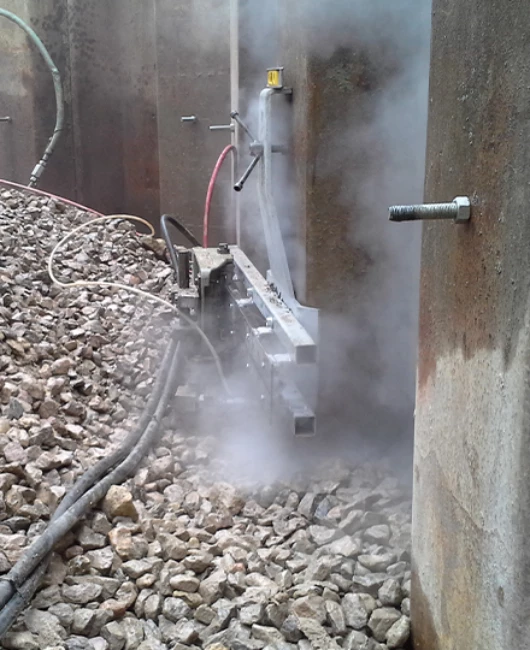
Work continued for four days cutting the in-pan sections of all piles. The out-pan cuts followed which took a further three days. These were undertaken in both dry and flooded conditions due to the rising river levels. It was imperative all the cuts lined up and this increased the set up time required for each cut. A small tang was left in 1 out of 3 out-pan cuts to support the cut piles prior to removal.
It was at this time that vertical cuts were undertaken. These were required as the clutches had been welded meaning the piles could not be slid apart as originally planned. The vertical cuts above the water level were gas burnt by Meller. These cuts were then continued under water by RGL to join the existing horizontal cuts made below the bed level.
The vertical cuts took an additional 2 days to complete. On day nine the removal of the cut pile sections began. They were removed in approximately 1.5 metre lengths (3 Larsen pile sections). Support strops were attached to the cut pile piece to ensure the pile was pulled away and carefully lifted by machine or hand, (depending on the access) as the holding tang was cut. RGL successfully completed the job on time and within budget. Once all pile sections were removed the river bund was released and normal water levels returned.
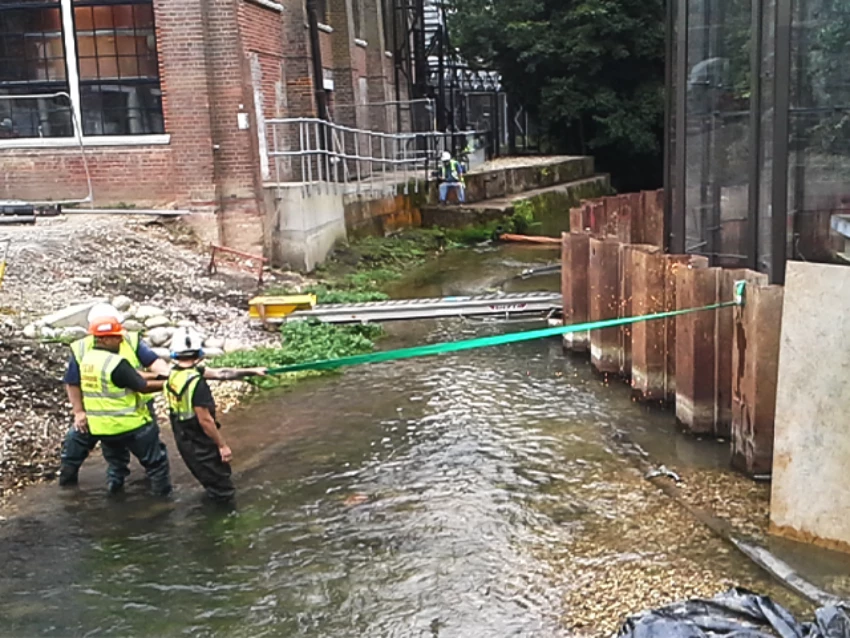
Request a call back