EDF - Hydrodemolition of Cooling Water Intake Jetty
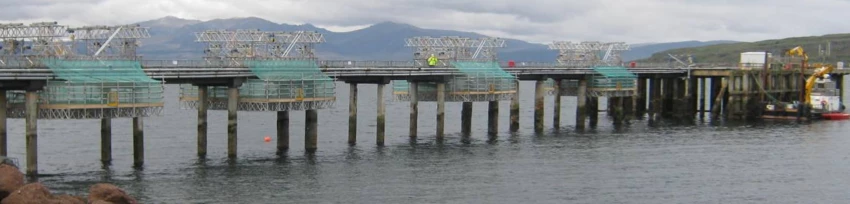
Precision hydrodemolition aides life-extending renovation of cooling water intake Jetty at Hunterston Nuclear Power Station
- Customer: EDF
- Service: Concrete hydrodemolition and Surface preparation
- Industry: Utilities and Power Generation
When inspections on the Cooling Water Intake Jetty at Hunterston Nuclear Power Station concluded that high chloride levels in the concrete from the marine environment had resulted in severe degradation, the Jetty became subject of a programme of work to repair and refurbish the structure, extending its use to 2024. RGL were invited to provide hydrodemolition services as the programme extended to work on the piles – readying them for repair.
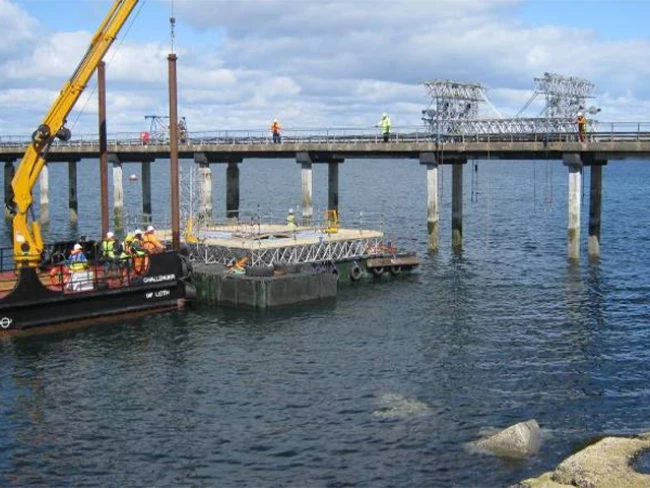
The initial programme involved repairs to the soffits, longitudinal beams and crossheads on the Jetty Arm, using purpose-built access platforms to aid the installation of a protective top coating. The coating acts to seal any ingress of water through the deck to the detriment of the structure.
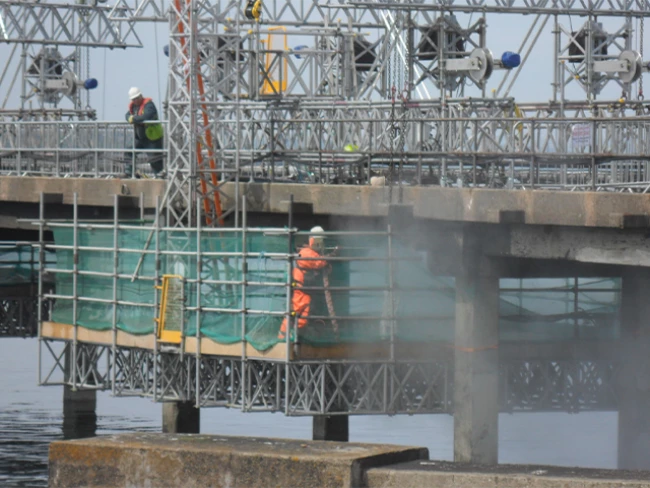
For owners EDF the extension of the station life meant a complete re-appraisal of planned structural maintenance to ensure that the facility could efficiently operate for another decade. One of the first programmes of work was the repair and refurbishment of the marine jetty which carries sea water intake to the nuclear plant for cooling purposes.
The jetty was originally built in 1959 and extended in 1976. The marine environment had resulted in high levels of chloride permeating the concrete and resulting in serious defects to the deck soffit, longitudinal beams and cross heads.
Mansell Concrete Repairs were appointed as the main contractor. They had to satisfy the requirements of EDF for the appointment of any sub-contractors – especially for a potentially high hazard application such as Hydrodemolition.
The Commercial Director, of RGL comments, “Although we had undertaken many projects for our contact at Mansell, it was understandable that EDF wanted to personally vet all subcontractors. We underwent a lengthy health/safety and quality pre-qualification check which involved a visit to our offices by a delegation from EDF. They met with our Operations Team to discuss our ideas on how this project could be undertaken.”
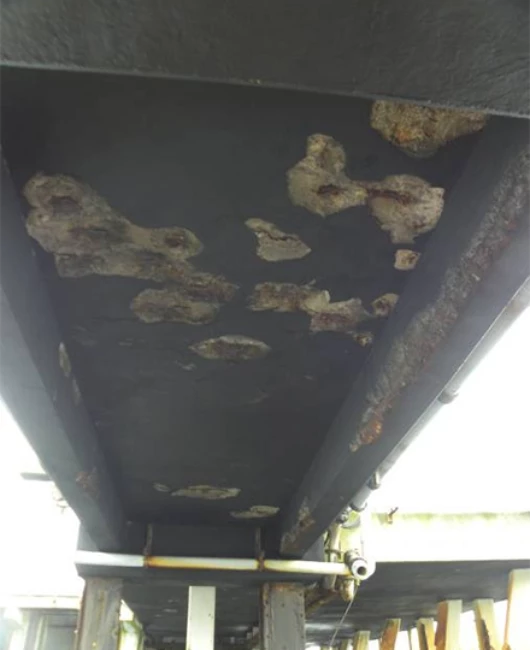
There were two key stages to the project. The first phase was to remove the failed bitumen protective coating from concrete surfaces under the structure. Once this had been completed there were about 30 cubic metres of defective concrete to be precision cut and removed using ultra high pressure Hydrodemolition.
RGL
proposed an innovative technical solution which employed a low flow ultra high
pressure water jet. By increasing the pressure up to 2,500bar it enabled RGL to
halve the water flow required. This resulted in a manageable and permissible
reaction force on the operators. This low reaction force meant that operators
suffered less work fatigue and it also reduced the risk of injury and
accidents.
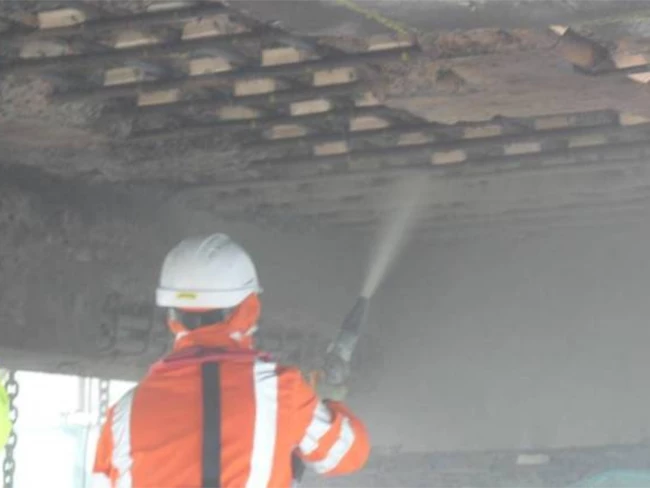
Furthermore it enabled the concrete to be cut out with a very high level of accuracy. It was this capability that led to a fundamental change in project scope and method of working.
“The added benefit of using UHP water jetting is that you can precision cut
concrete. Once you get up to 2,500bar it is possible to cut the rock
aggregate not just the cement matrix. It is also possible to cut to a
finer tolerance, again without damaging the steel reinforcement.
“Soon after the project began we determined that instead of removing all the concrete from the bay soffits, it would be more cost effective to precision cut patches of defective concrete. It is essential to cut back behind the first layer of steel reinforcement to ensure maximum strength and integrity of the repair.”
Consequently the project was re-scoped from mass high volume concrete removal to a targeted repair approach which required a greater level of plant and operative mobility as they switched from one bay to another to help maintain structural strength of the jetty.
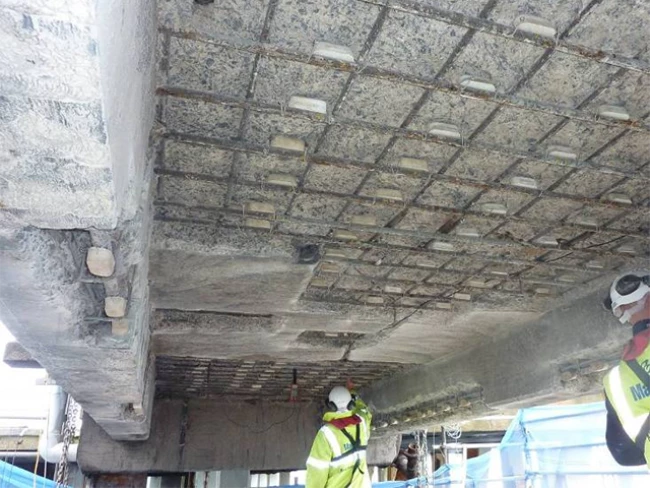
Paul Franklin, Operations Manager, Mansell Concrete Repairs, comments, “From the outset Mansell Concrete Repairs knew that to secure the project with EDF a solid team would have to be assembled. We called RGL as we have known them for many years as a reputable and resourceful water jetting specialist. They wholeheartedly embraced the stringent and lengthy Health Safety and Environmental Audit process, firstly with ourselves and then EDF. The “Precision Hydrodemolition” process worked well and greatly assisted Mansell in providing our client with a high quality refurbishment of this critical structure whilst meeting our group goal of “Zero Harm”.”
On the Hunterston project RGL incorporated many of their key capabilities – technical innovation, reliability, project flexibility and excellent health and safety management – on a key part of the national energy infrastructure, where the stakes were high.
If you would like to know more about our underwater Hydrodemolition services, Contact RGL today.
Request a call back