DBB - Underwater Pile Cutting of Met Mast Monopiles
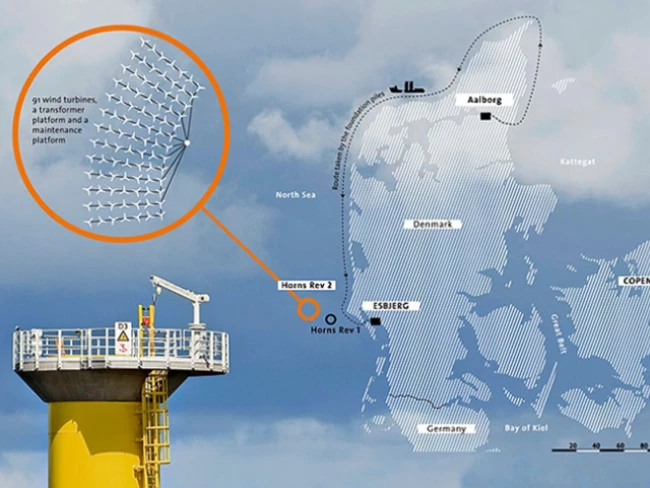
- Customer: DBB Jack-Up Services A/S
- Service: Abrasive Water Jet Cold Cutting / Underwater Pile Cutting
- Industry: Marine structures, Maritime and Offshore
When DBB Jack up Services A/S tendered to remove a Monopile from Horns Rev, Offshore Denmark. RGL were selected as the ideal partner to provide the underwater pile cutting services.
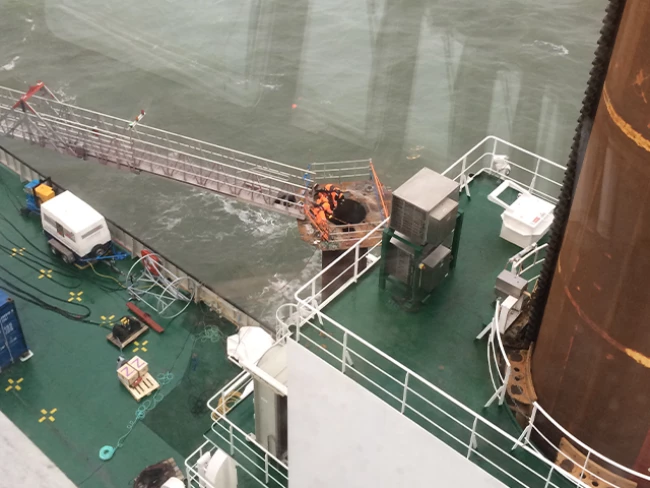
Preparation
After some initial discussion and meetings RGL provided a quotation for the project DBB were subsequently successful in their tender submission for the project.
RGL’s Commercial Director Jeremy Twigg and Team Leader for the project visited Denmark in advance of the works to undertake a detailed site survey of the Monopile with DBB.
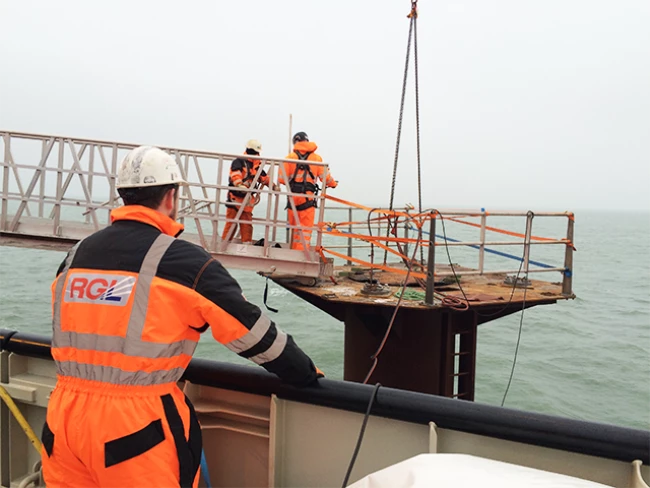
This enabled the relationships between DBB and RGL to strengthen and ensured both company's’ understood their individual role with the project scope for the project. For RGL this included the dredging of material from within the pile, the proving and cleaning of pile internal prior to cutting the Monopile at a depth of 24.2 metres. DBB had just taken delivery of their brand new Jack Up Vessel: WIND SERVER. This is a very impressive vessel with lifting capacity of 400 tonne and cutting edge technology. It has capability to jack up in 45 metres of water. Before any works inside the pile were possible a steel deck plate needed to be removed to allow access to the Monopile
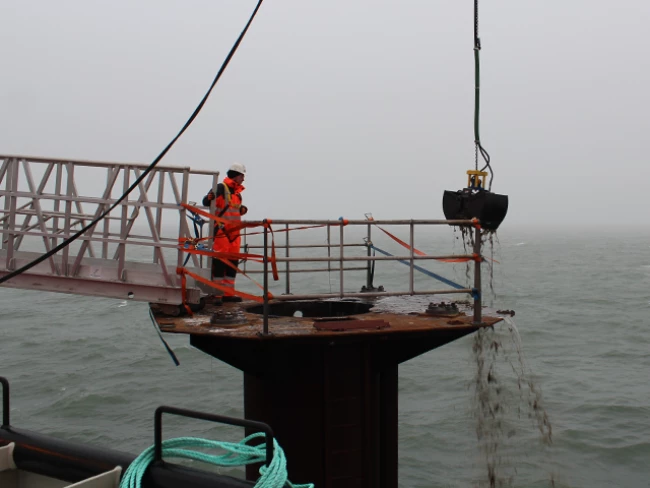
Dredging
The initial phase of works was to dredge material from inside the pile to approximately 1 metre below the agreed cut line. This was achieved by using a clamshell excavator bucket and dredger pump. After successfully removing all hard objects the dredger pump with UHP jet injection assistance was employed to empty sand and other fine material from within the pile.
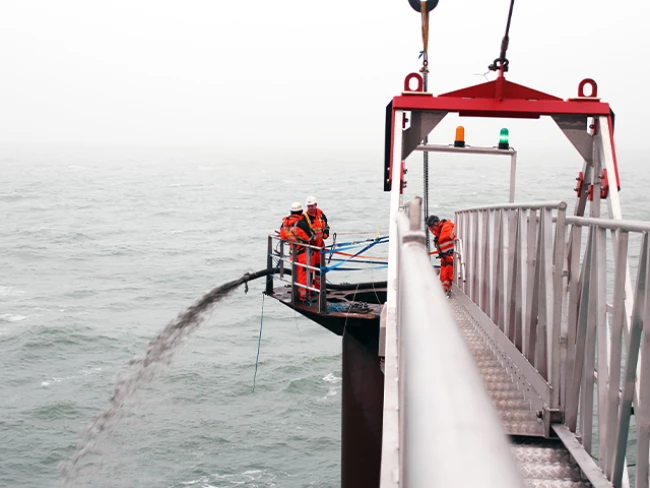
Several cubic metres of sand were removed. This process was very effective and the pump was repositioned several times around the pile until the depth of dredge was achieved. After dipping, a strange profile was discovered with depth variations of 200-600mm. Initially it was thought the pump was digging holes in a hard sub base; however when the clam shell was used to investigate this anomaly, steel coupons were found to be causing the problem. These were then removed allowing the dredging process to be completed.
Proving
Upon completion of the dredging, the custom made proving rig was deployed. This equipment was designed to confirm the pile had no internal obstructions. The proving rig was lowered 4 times in total, each time to a depth of 25 metres. The proving rig was fitted with a rotating High Pressure Water Jet Nozzle to enable the cleaning of the internal bore simultaneously, whilst proving the internal diameter. Once this process was complete the pile was ready for rigging with lifting equipment.
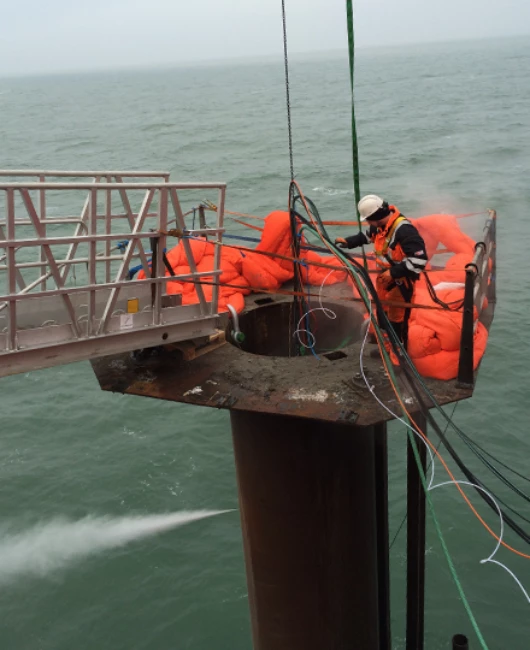
Cutting
The RGL cutting rig was lowered into the pile and a test cut close to the top of the pile was made. After successfully completing this cut, preparations for the main cut at depth were made. As the cutting rig was lowered into the pile all service hoses and lines were clamped together. The JackUp WIND SERVER itself was raised 2.5 metres to bring it level with the pile to give safe access for the installation process. Water depth was approximately 14 metres.
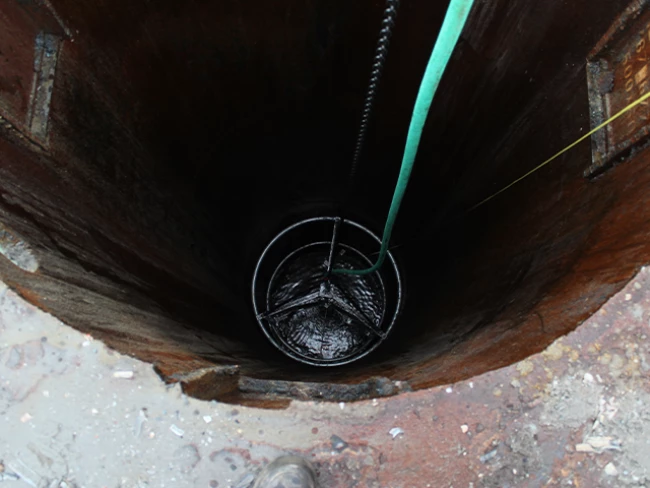
The cut line was set to 24.2 metres from the top of the pile. It took 8 hours to complete. This involved working well into the night before the successfully cut pile was lifted clear of the water. The 44 tonnes of pile was placed onto the deck of the WIND SERVER where it was possible to see the near perfect cut achieved by RGL through the 45mm wall. The previous diamond wire sawing attempts were also visible; this method had originally been attempted, but had proven unsuccessful.
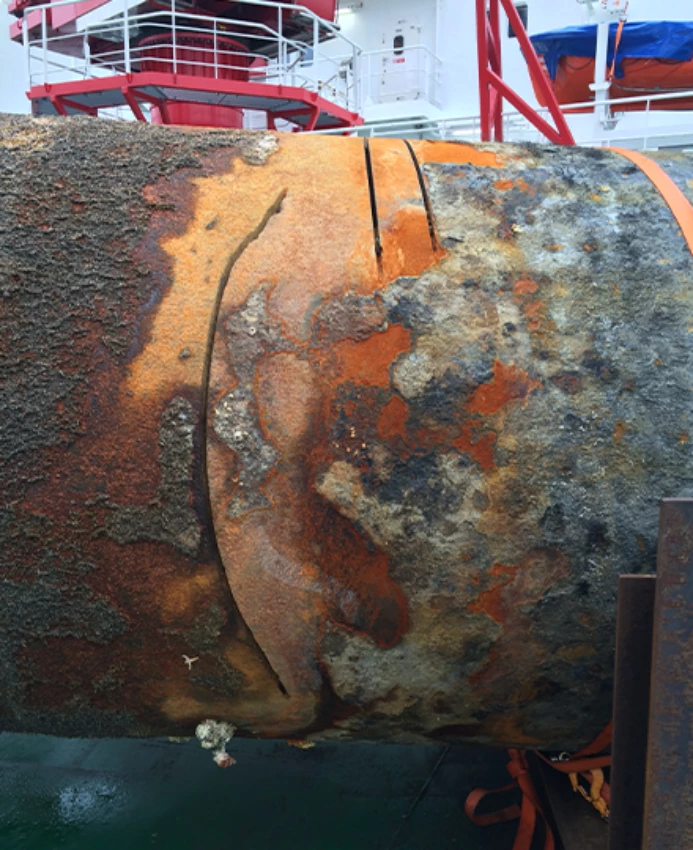
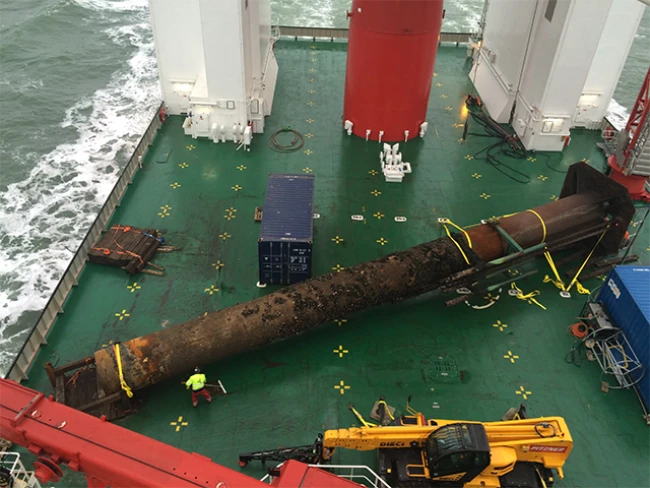
Anders Thorvald Nielsen, Operations Manager for DBB commented: “DBB was extremely satisfied with the performance, preparation and result of the RGL operation. RGL crew was well prepared and very pleasant to work with. A job well done”.
Request a call back