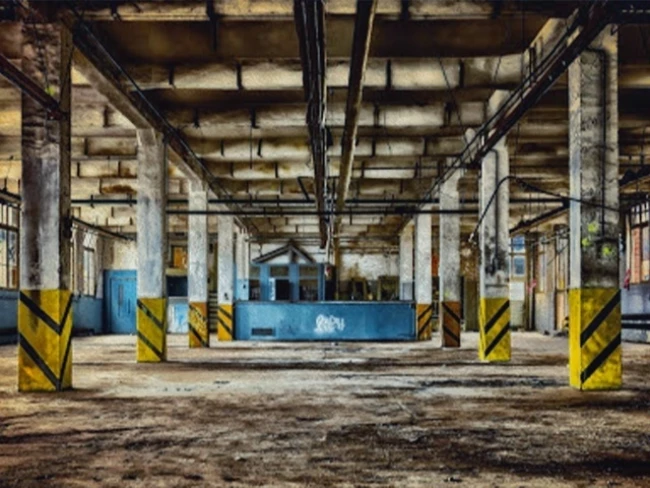
Civil Engineering
Tanks and vessels are full of hard to reach areas. Fortunately, our high pressure (up to 1500bar) water tank jetting heads rotate on their own axis to remove hard compounds and provide a thorough clean, without the need for operatives to enter these confined spaces.
Our water jet tank and vessel cleaning services are available for all types of industrial process plant, even food or medical grade tank systems.
Avoid manned entry cleaning and protect your workforce from unnecessary dangers. We offer a fast and efficient service, ensuring your equipment is quickly restored to optimum working capacity with minimal downtime during the cleaning process.
Heat exchangers and condenser tube bundles slowly become less efficient because of the build-up of scale or by-product. They need careful cleaning because they are fragile and expensive tube materials. Drilling or mechanical cleaning techniques can deform or even split the tubes. The use of chemical cleaning is very often not an option in a food production environment. UHP water jetting using just clean potable water is therefore a very practical solution to these problems.
We can either clean heat exchangers on site or we can provide facilities for accepting and cleaning exchangers at our head office in Southampton – usually with a very fast turnaround to keep outages to a minimum.
Some of our toughest challenges to date:
Our Rotoream™ pipeline cleaning machine is often deployed to clean long lengths of production pipeline with multiple bends, usually where a blockage has occurred or there has been a mechanical malfunction.
One of our soft drink manufacturers asked us to overcome the problem of a failed seal which had let food grade grease into a very long and complicated production ring main. Our specialist equipment was able to remove all traces of the grease to leave a perfectly clean inner tube.
Another client did not want to access the pipe network over their food production areas and our Rotoream™ machine was able to clear the blockage from a maintenance point outside the production area – once again this involved negotiating long lengths of pipes with multiple bends.
Great work can only come from great partnerships. Here are just a few of the amazing customers that have challenged us to find a water jetting solution, and we've delivered.
Other industries
Over 40 years, we have turned our knowledge of water jetting technology into a range of cutting, cleaning, surface preparation and hydrodemolition services - ideally suited to the task and industry at hand.
Civil Engineering
Water, Sewage and Environmental
RGL are the UK’s leading interface between water jetting technology and the job to be done.
Call us on 02380 817 172 or request a call back
We use Cookies!
This website uses essential cookies to ensure its proper operation and tracking cookies to understand how you interact with it. The latter will be set only after consent.